Gramophone record -- Long Play records
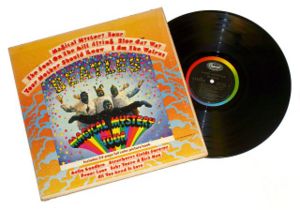
A gramophone record (also phonograph record, or simply record) is an analogue sound recording medium consisting of a flat disc with an inscribed modulated spiral groove starting near the periphery and ending near the center of the disc. Gramophone records were the primary technology used for personal music reproduction for most of the 20th century. They replaced the phonograph cylinder in the 1900s, and although they were supplanted in popularity in the late 1980s by digital media, they continue to be manufactured and sold.
The terms LP record (LP, 33, or 33-1/3 rpm record), 16 rpm record (16), 45 rpm record (45), and 78 rpm record (78) each refer to specific types of gramophone records. Except for the LP, these type designations refer to their rotational speeds in revolutions per minute (RPM). LPs, 45s, and 16s are usually made of polyvinyl chloride (PVC), and hence may be referred to as vinyl records or simply vinyl.
History
Early history
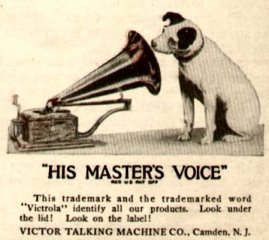
A sound recording and reproduction device utilizing what were essentially disc records was described by Charles Cros of France in 1877 but never built. In 1878, Thomas Edison independently built the first working phonograph, a tinfoil cylinder machine. He intended it to be used as a voice recording medium, typically for office dictation. The phonograph cylinder dominated the recorded sound market beginning in the 1880s. Lateral-cut disc records were invented by Emile Berliner in 1888 and were used exclusively in toys until 1894, when Berliner began marketing disc records under the Berliner Gramophone label. The Edison "Blue Amberol" cylinder was introduced in 1912, with a longer playing time of around 4 minutes (at 160 rpm) and a more resilient playing surface than its wax predecessor, but the format was doomed due to the difficulty of reproducing recordings. By November 1918 the patents for the manufacture of lateral-cut disc records expired, opening the field for countless companies to produce them, causing disc records to overtake cylinders in popularity. They would dominate the market until the 1980s. Production of Amberol cylinders ceased in the late 1920s.
Materials
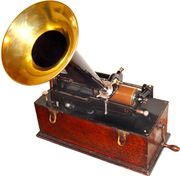
Early disc records were originally made of various materials including hard rubber. From 1897 onwards, earlier materials were largely replaced by a rather brittle formula of 25% "shellac" (a material obtained from the excretion of a southeast Asian beetle), a filler of a cotton compound similar to manila paper, powdered slate and a small amount of a wax lubricant. The mass production of shellac records began in 1898 in Hanover, Germany. Shellac records were the most common until the 1950s. Unbreakable records, usually of celluloid (an early form of plastic) on a pasteboard base, were made from 1904 onwards, but they suffered from an exceptionally high level of surface noise.
In the 1890s the early recording formats of discs were usually seven inches (nominally 17.5 cm) in diameter. By 1910 the 10-inch (25.4cm) record was by far the most popular standard, holding about three minutes of music or entertainment on a side. From 1903 onwards, 12-inch records (30.5cm) were also commercially sold, mostly of classical music or operatic selections, with four to five minutes of music per side.
Such records were usually sold separately, in plain paper or cardboard sleeves that may have been printed to show producer of the retailer's name and, starting in the 1930's, in collections held in paper sleeves in a cardboard or leather book, similar to a photograph album, and called record albums. Empty record albums were also sold that customers could use to store their records in.
While a 78 rpm record is brittle and relatively easily broken, both the microgroove LP 33⅓ rpm record and the 45 rpm single records are made from vinyl plastic which is flexible and unbreakable in normal use. However, the vinyl records are easier to scratch or gouge. 78s come in a variety of sizes, the most common being 10 inch (25 cm) and 12 inch (30 cm) diameter, and these were originally sold in either paper or card covers, generally with a circular cutout allowing the record label to be seen. The Long-Playing records (LPs) usually come in a paper sleeve within a colour printed card jacket which also provides a track listing. 45 rpm singles and EPs (Extended Play) are of 7 inch (17.5 cm) diameter, the earlier copies being sold in paper covers.
In 1930, RCA Victor launched the first commercially available vinyl long-playing record, marketed as "Program Transcription" discs. These revolutionary discs were designed for playback at 33⅓ rpm and pressed on a 30 cm diameter flexible plastic disc. In Roland Gelatt's book The Fabulous Phonograph, the author notes that RCA Victor's early introduction of a long-play disc was a commercial failure for several reasons including the lack of affordable, reliable consumer playback equipment and consumer wariness during the Great Depression.[1]
However, vinyl's lower surface noise level than shellac was not forgotten, nor was its durability. In the late 30's, radio commercials and pre-recorded radio programs being sent to disc jockies started being stamped in vinyl, so they would not break in the mail. In the mid-40's, special DJ copies of records started being made of vinyl also, for the same reason. These were all 78 RPM. During and after World War II when shellac supplies were extremely limited, some 78 rpm records were pressed in vinyl instead of shellac (wax), particularly the six-minute 12" (30 cm) 78 rpm records produced by V-Disc for distribution to US troops in World War II. In the 40's, radio transcriptions, which were usually on 16 inch records, but sometimes 12 inch, were always made of vinyl, on 78 RPM.
Beginning in 1939, Columbia Records continued development of this technology. Dr. Peter Goldmark and his staff undertook exhaustive efforts to address problems of recording and playing back narrow grooves and developing an inexpensive, reliable consumer playback system. In 1948, the 12" (30 cm) Long Play (LP) 33⅓ rpm microgroove record album was introduced by the Columbia Record at a dramatic New York press conference. In 1949, RCA Victor released the first 45 RPM single, 7" in diameter, with a large center hole to accommodate an automatic play mechanism on the changer, so a stack of singles would drop down one record at a time automatically after each play.

During the reign of the Communist Party in the former USSR, records were commonly homemade using discarded medical x-rays. These records, nicknamed "Bones", were usually inscribed with illegal copies of popular music banned by the government. They also became a popular means of distribution among Soviet punk bands; in addition to the high cost and low availability of vinyl, punk music was politically suppressed, and publishing outlets were limited.
Speeds
Earliest rotation speeds varied widely, but between 1900-1925 most records were recorded between 74-82 rpm. In 1925, 78.26 rpm was chosen as the standard because of the introduction of the electrically powered synchronous turntable motor. This motor ran at 3600 rpm with a 46:1 gear ratio which produced 78.26 rpm. In parts of the world that used 50 Hz current, the standard was 77.92 RPM, which was the speed at which a strobe disc with 77 lines would "stand still" in 50 Hz light. Thus these records became known as 78s (or "seventy-eights"). This term did not come into use until after World War II when a need developed to distinguish the 78 from other newer disc record formats, an example of a retronym. Earlier they were just called records, or when there was a need to distinguish them from cylinders, disc records. Standard records was also used, although the same term had also been used earlier for two-minute cylinders.
After World War II, two new competing formats came on to the market and gradually replaced the standard "78": the 33⅓ rpm (often just referred to as the 33 rpm), and the 45 rpm. The 33⅓ rpm LP (for "long play") format was developed by Columbia Records and marketed in 1948. RCA Victor developed the 45 rpm format and marketed it in 1949, in response to Columbia. Both types of new disc used narrower grooves, intended to be played with a smaller stylus - typically 0.001" (25 µm) wide, compared to 0.003" (76 µm) for a 78 - so the new records were sometimes called Microgroove. In the mid-1950s all record companies agreed to a common recording standard called RIAA equalization. Prior to the establishment of the standard each company used its own preferred standard, requiring discriminating listeners to use preamplifiers with multiple selectable equalization curves.
A number of recordings were pressed at 16⅔ RPM, but these were mostly used for radio transcription discs or narrated publications for the blind and visually impaired, and were never widely commercially available.
The older 78 format continued to be mass produced alongside the newer formats into the 1950s, and in a few countries, such as India, into the 1960s. As late as the 1970s, some children's records were released at the 78 rpm speed.
The commercial rivalry between RCA Victor and Columbia Records led to RCA Victor's introduction of what it had intended to be a competing vinyl format, the 7" (175 mm) /45 rpm disc. For a two-year period from 1948 to 1950, record companies and consumers faced uncertainty over which of these formats would ultimately prevail in what was known as the "War of the Speeds". (See also format war)
Eventually the 12" (300 mm) 33⅓ rpm LP prevailed as the predominant format for musical albums, and the 7" (175 mm) 45 rpm disc or "single" established a significant niche for shorter duration discs, typically containing one song on each side. The 45 rpm discs typically emulated the playing time of the former 78 rpm discs, while the LP discs provided up to one half hour of time per side (though typically 15 to 20 minutes). The 45 rpm discs also came in a variety known as Extended play (EP) which achieved up to 25 minutes play at the expense of attenuating (and possibly compressing) the sound to reduce the width required by the groove.
From the mid-1950s through the 1960s, in the US the common home "record player" or "stereo" would typically have had these features: a three- or four-speed player with changer (78, 45, 33⅓, and sometimes 16⅔ rpm); a combination cartridge with both 78 and microgroove styluses; and some kind of adapter for playing the 45s with their larger center hole. The large center hole on 45s allows for easier handling by jukebox mechanisms. RCA 45s can also be adapted to the smaller spindle of an LP player with a plastic snap-in insert known as a 'spider'; such inserts were prevalent starting in the 1960s.
Deliberately playing or recording records at the wrong speed was a common amusement. For example, playing the song "I'm on Fire" from Bruce Springsteen's 33⅓ LP at a 45 speed gives the singer a falsetto singing voice that sounds very much like Dolly Parton. Subsequently, playing a 45 rpm recording of Dolly Parton at 33⅓ gives her a voice a husky, almost masculine tone.
Canadian musician Nash the Slash took advantage of this speed/tonal effect with his 1981 12" disc Decomposing, which featured four instrumental tracks that were engineered to play at any speed (with the playing times listed for 33⅓, 45 and 78 rpm playback). Faster playback made the tracks sound like punk rock or power pop, while slower speeds gave the songs a thick, heavy metal effect.
Explanation
The normal commercial disc is engraved with two sound bearing concentric spiral grooves, one on each side of the disc, running from the outside edge towards the centre. Since the late 1910s, both sides of the record have been used to carry the grooves. The recording is played back by rotating the disc clockwise at a constant rotational speed with a stylus (needle) placed in the groove, converting the vibrations of the stylus into an electric signal (see magnetic cartridge), and sending this signal through an amplifier to loudspeakers.
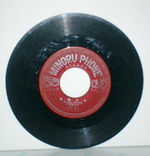
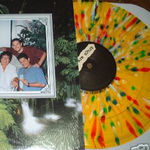
Common formats
- 12" (30 cm) 33⅓ rpm long-playing (LP) format
- 12" (30 cm) 45 rpm extended-playing (12-inch (30 cm) single, Maxi Single and EP) format
- 12" (30 cm) 78 rpm format, 4-5 minutes
- 10" (25 cm) 78 rpm format, 3 minutes
- 7" (17.5 cm) 45 rpm (single) format
- 7" (17.5 cm) 45 rpm extended-playing (EP) format
Less common formats
Structure of a typical record
The majority of records are pressed on black vinyl. The colouring material used to blacken the transparent PVC plastic mix is carbon black, the generic name for the finely divided carbon particles produced by the incomplete burning of a mineral oil based hydrocarbon. Carbon black increases the strength of the disc and renders it opaque.
Some records are pressed on coloured vinyl or with paper pictures embedded in them ("picture discs"). These discs can become collectors' items in some cases. During the 1980s there was a trend for releasing singles on colour vinyl— sometimes with large inserts that could be used as posters. This trend has been revived recently and has succeeded in keeping 7" singles a viable format.
Vinyl record standards for the United States follow the guidelines of the Recording Industry Association of America (RIAA).[2] The inch dimensions are nominal, not precise diameters. The actual dimension of a 12 inch record is 302 mm (11.89 in), for a 10 inch it is 250 mm (9.84 in), and for a 7 inch it is 175 mm (6.89 in).
Records made in other countries are standardized by different organizations, but are very similar in size. The record diameters are typically 300 mm, 250 mm and 175 mm.
There is an area about 6 mm (0.25″) wide at the outer edge of the disk, called the lead-in where the groove is widely spaced and silent. This section allows the stylus to be dropped at the start of the record groove, without damaging the recorded section of the groove.
Between each track on the recorded section of an LP record, there is usually a short gap of around 1 mm (0.04") where the groove is widely spaced. This space is clearly visible, making it easy to find a particular track.
Towards the label centre, at the end of the groove, there is another wide-pitched section known as the lead-out. At the very end of this section, the groove joins itself to form a complete circle, called the lock groove; when the stylus reaches this point, it circles repeatedly until lifted from the record. Automatic turntables rely on the position or angular velocity of the arm, as it reaches these more widely spaced grooves, to trigger a mechanism that raises the arm and moves it out of the way of the record.
The catalog number and stamper ID is written or stamped in the space between the groove in the lead-out on the master disc, resulting in visible recessed writing on the final version of a record. Sometimes the cutting engineer might add handwritten comments or their signature, if they are particularly pleased with the quality of the cut.
When auto-changing turntables were commonplace, records were typically pressed with a raised (or ridged) outer edge and label area. This would allow records to be stacked onto each other, gripping each other without the delicate grooves coming into contact, thus reducing the risk of damage. Auto changing turntables included a mechanism to support a stack of several records above the turntable itself, dropping them one at a time onto the active turntable to be played in order. Many longer sound recordings, such as complete operas, were interleaved across several 10-inch or 12-inch discs for use with auto-changing mechanisms, so that the first disk of a three-disk recording would carry sides 1 and 6 of the program, while the second disk would carry sides 2 and 5, and the third, sides 3 and 4, allowing sides 1, 2, and 3 to be played automatically, then the whole stack reversed to play sides 4, 5, and 6.
Progress, and the war of the speeds
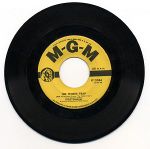
About the same time the most common substance for making 33 rpm disc records became vinyl, while 45 rpm discs were made from either vinyl or polystyrene. All speeds of records were made in various sizes, mainly 17.5, 25, 30 cm (~7, 10 and 12 inches diameter); the 17.5 cm (~7-inch) being most common for the 45 rpm, the 25 cm (~10-inch) for the 78 (and the first few years of 33⅓ production), and the 30 cm (~12-inch) for the 33 from the mid 1950s on.
Vinyl quality
The sound quality and durability of vinyl records is highly dependent on the quality of the vinyl. During the early 1970s, as a cost-cutting move towards use of lightweight, flexible vinyl pressings, much of the industry adopted a technique of reducing the thickness and quality of vinyl used in mass-market manufacturing, marketed by RCA Victor as the "Dynaflex" (125 g/m²) process. Most vinyl records are pressed on recycled vinyl.
New "virgin" or "heavy" (180-220 g/m²) vinyl is commonly used for classical music, although it has been used for some other genres. Today, it is increasingly common in vinyl pressings that can be found in most record shops. Many classic rock albums have been reissued on 180 g/m² vinyl. Modern albums are also commonly pressed on 180 g/m². Many collectors prefer to have 180 gram vinyl albums, and they have been reported to have a better sound than normal vinyl. These albums tend to withstand the deformation caused by normal play better than regular vinyl.
Since most vinyl records are from recycled plastic, it can lead to impurities in the record, causing a brand new album to have audio artifacts like clicks and pops. Virgin vinyl means that the album is not from recycled plastic, and will be devoid of the possible impurities of recycled plastic.
While most vinyl records are pressed from metal master discs, a technique known as lathe-cutting was introduced in the late 1980s by Peter King in Geraldine, New Zealand.[3] A lathe is used to cut microgrooves into a clear polycarbonate disc. Lathe cut records can be made inexpensively in small runs. However, the sound quality is significantly worse than proper vinyl records, and lathe cut records tend to degrade further in quality after repeated playing.
Stereo and beyond
In 1958 the first stereo two-channel records were issued – by Audio Fidelity in the USA and Pye in Britain, using the Westrex "45/45" single-groove system. While the stylus moves horizontally when reproducing a monophonic disk recording, on stereo records the stylus moves vertically as well as horizontally.
One could envision a system in which the left channel was recorded laterally, as on a monophonic recording, with the right channel information recorded with a "hill-and-dale" vertical motion; such systems were proposed but not adopted, due to their incompatibility with existing phono pickup designs (see below). In the Westrex system, each channel drives the cutting head at a 45 degree angle to the vertical. During playback the combined signal is sensed by a left channel coil mounted diagonally opposite the inner side of the groove, and a right channel coil mounted diagonally opposite the outer side of the groove.[4]
It is helpful to think of the combined stylus motion in terms of the vector sum and difference of the two stereo channels. Effectively, all horizontal stylus motion conveys the L+R sum signal, and vertical stylus motion carries the L-R difference signal. The advantages of the 45/45 system are:
- greater compatibility with monophonic recording and playback systems. A monophonic cartridge will reproduce an equal blend of the left and right channels instead of reproducing only one channel. Conversely, a stereo cartridge reproduces the lateral grooves of monophonic recording equally through both channels, rather than one channel.
- a more balanced sound, because the two channels have equal fidelity (rather than providing one higher-fidelity laterally recorded channel and one lower-fidelity vertically recorded channel);
- higher fidelity in general, because the "difference" signal is usually of low power and thus less affected by the intrinsic distortion of hill-and-dale recording.
This system was invented by Alan Blumlein of EMI in 1931 and patented the same year. EMI cut the first stereo test discs using the system in 1933. It was not exploited commercially until a quarter of a century later.
Stereo sound provides a more natural listening experience where the spatial location of the source of a sound is, at least in part, reproduced.
The development of quadraphonic records was announced in 1971. These recorded four separate sound signals. This was achieved on the two stereo channels by electronic matrixing, where the additional channels were combined into the main signal. When the records were played, phase-detection circuits in the amplifiers were able to decode the signals into four separate channels. There were two main systems of matrixed quadrophonic records produced, confusingly named SQ (by CBS) and QS (by Sansui). They proved commercially unsuccessful, but were an important precursor to later 'surround sound' systems, as seen in SACD and home cinema today. A different format, CD-4 (not to be confused with compact disc), by RCA, encoded rear channel information on an ultrasonic carrier, which required a special wideband cartridge to capture it on carefully-calibrated pickup arm/turntable combinations. Typically the high frequency information inscribed onto these LPs wore off after only a few playings, and CD-4 was even less successful than the two matrixed formats.
Other developments
Under the direction of C. Robert Fine, Mercury Records initiated a minimalist single microphone monaural recording technique in 1951. The first record, Kubelik/Chicago's performance of "Pictures at an Exhibition" was described as "being in the living presence of the orchestra" by the NY Times music critic. The series of records was then named “Mercury Living Presence.” In 1955 Mercury began 3-channel stereo recordings, still based on the principle of the single microphone. The center (single) mic was of paramount importance, with the two side mics adding depth and space. Record masters were cut directly from a 3-track to 2-track mixdown console, with all editing of the master tapes done on the original 3-tracks. In 1961 Mercury enhanced this technique with three-microphone stereo recordings using 35mm magnetic film instead of half-inch tape for recording. The greater thickness and width of 35mm magnetic film prevented tape layer print-through and pre-echo and gained extended frequency range and transient response. The Mercury Living Presence recordings were remastered to CD in the 1990s by the original producer, using the same method of 3-to-2 mix directly to the master recorder.
On a small number of early phonograph systems and radio transcription discs, as well as some entire albums, such as Goodbye Blue and White by Less Than Jake, the direction of the groove is reversed, beginning near the centre of the disc and leading to the outside. A small number of records (such as Jeff Mills' Apollo EP or the Hidden In Plainsight EP from Detroit's Underground Resistance) were manufactured with multiple separate grooves to differentiate the tracks (usually called 'NSC-X2'). X2 was pioneered by Ron Murphy and Heath Brunner from Sound Enterprises (formerly National Sound Corporation), a record mastering company in Detroit.
In the late 1970s "direct-to-disc" records were produced, aimed at an audiophile niche market. These completely bypassed the use of magnetic tape in favor of a "purist" transcription directly to the master lacquer disc. Also during this period, "half-speed mastered" and "original master" records were released, using expensive state-of-the-art technology.
The early 1980s saw the introduction of "dbx-encoded" records, again for the audiophile niche market. These were completely incompatible with standard record playback preamplifiers, relying on the dbx compandor encoding/decoding scheme to greatly increase dynamic range (dbx encoded disks were recorded with the dynamic range compressed by a factor of two in dB: quiet sounds were meant to be played back at low gain and loud sounds were meant to be played back at high gain, via automatic gain control in the playback equipment; this reduced the effect of surface noise on quiet passages). A similar and very short lived scheme involved using the CBS-developed "CX" noise reduction encoding/decoding scheme.
Also in the late 1970s and 1980s, a method to improve the dynamic range of mass produced records involved highly advanced disc cutting equipment. These techniques, marketed as the CBS Discomputer and Teldec Direct Metal Mastering, were used to reduce inner-groove distortion.
ELPJ, a Japanese-based company, has developed a player that uses a laser instead of a stylus to read vinyl discs. In theory the laser turntable eliminates the possibility of scratches and attendant degradation of the sound, but its expense limits use primarily to digital archiving of analog records. Various other laser-based turntables were tried during the 1990s, but while a laser reads the groove very accurately, since it does not touch the record, the dust that vinyl naturally attracts due to static charge is not cleaned from the groove, worsening sound quality in casual use compared to conventional stylus playback.
Record mastering and pressing
Recording the disc
For the first several decades of disc record manufacturing, sound was recorded directly on to the master disc (also called the matrix, sometimes just the master) at the recording studio. From about 1950 on (earlier for some large record companies, later for some small ones) it became usual to have the performance first recorded on audio tape, which could then be processed and/or edited, and then dubbed on to the master disc.
A record cutter would engrave the grooves into the master disc. Early versions of these master discs were soft wax, and later a harder lacquer was used.
The mastering process was originally something of an art as the operator had to manually allow for the changes in sound which affected how wide the space for the groove needed to be on each rotation. Sometimes the engineer would sign his work, or leave humorous or cryptic comments in the run-off groove area, where it was normal to scratch or stamp identifying codes to distinguish each master.
[edit] Mass producing records
The soft master known as a lacquer would then be electroplated with a metal, commonly a nickel alloy. This and all subsequent metal copies were known as matrices. When this metal was removed from the lacquer (master), it would be a negative master since it was a negative copy of the lacquer. (In the UK, this was called the master; note the difference from soft master/lacquer disc above). In the earliest days the negative master was used as a mold to press records sold to the public, but as demand for mass production of records grew, another step was added to the process.
The metal master was then electroplated to create metal positive matrices, or "mothers". From these negatives, stampers would be formed. The stampers would be used in hydraulic presses to mould the LP discs. The advantages of this system over the earlier more direct system included ability to make a large number of records quickly by using multiple stampers. Also, more records could be produced from each master since molds would eventually wear out.
Since the master was the unique source of the positive, made to produce the stampers, it was considered a library item. Accordingly, copy positives, required to replace worn positives, were made from unused early stampers. These were known as copy shells and were the physical equivalent of the first positive.
The "pedigree" of any record can be traced through the stamper/positive identities used, by reading the lettering found on the record run-out area.
Packaging and distribution
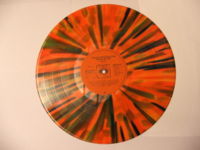
Singles are typically sold in plain paper wrappers, though EPs are often treated to a cover in similar style to an LP. LPs are universally packaged in cardboard covers with a paper liner protecting the delicate surface of the record. Also, with the advent of long-playing records, the album cover became more than just packaging and protection, and album cover art became an important part of the music marketing and consuming experience. In the 1970s it became more common to have picture covers on singles. However, many singles with picture sleeves (especially from the 1960s) are sought out by collectors, and the sleeves alone can go for a high price. LPs can have embossed cover art (with some sections being raised), an effect rarely seen on CD covers.
Records are made at large manufacturing plants, either owned by the major labels, or run by independent operators to whom smaller operations and independent labels could go for smaller runs. A band starting out might get a few hundred disks stamped, whereas big selling artists need the presses running full time to manufacture the hundreds of thousands of copies needed for the launch of a big album.
Records are generally sold through specialist shops, although some big chain stores also have record departments. Many records are sold from stock, but it is normal to place special orders for less common records. Stock is expensive, so only large city center stores can afford to have several copies of a record.
Record labels
Record companies organised their products into labels. These could either be subsidiary companies, or they could simply be just be a brand name. For example, EMI published records under the His Master's Voice (HMV) label which was their classical recording brand, Harvest for their progressive rock brand, home to Pink Floyd. They also had Music for Pleasure and Classics for Pleasure as their economy labels. EMI also used the Parlophone brand in the UK for Beatles records in the early 1960's.
In the 1970's successful musicians sought greater control, and one way they achieved this was with their own labels, though normally they were still operated by the large music corporations. Two of the most famous early examples of this were the Beatles' Apple Records and Led Zeppelin's Swan Song Records
In the late 1970's the anarchic punk rock movement gave rise to the independent record labels. These were not owned or even distributed by the main corporations. In the UK, examples were Stiff Records who published Ian Dury and the Blockheads and Two Tone Records, label for The Specials. These allowed smaller bands to step onto the ladder without having to conform to the rigid rules of the large corporations.
Disc limitations
Shellac
Shellac 78's are brittle, and must be handled carefully. In the event of a 78 breaking, the pieces might remain loosely connected by the label and still be playable if the label holds them together, although there is a loud 'pop' with each pass over the crack, and breaking of the needle is likely.
Breakage was a very common accident in the shellac era. In the 1934 novel, Appointment in Samarra, the protagonist "broke one of his most favorites, Whiteman's Lady of the Evening ... He wanted to cry but could not." A poignant moment in J. D. Salinger's 1951 novel The Catcher in the Rye occurs after the adolescent protagonist buys a record for his younger sister but drops it and "it broke into pieces ... I damn near cried, it made me feel so terrible."
[edit] Vinyl
Vinyl records do not break easily, but the soft material is easily scratched. Vinyl readily acquires a static charge, attracting dust that is difficult to remove completely. Dust and scratches cause audio clicks and pops. In extreme cases, they can cause the needle to skip over a series of grooves, or worse yet, cause the needle to skip backwards, creating a "locked groove" that repeats the same 1.8 seconds of track (at 33⅓ rpm) over and over again. Locked grooves were not uncommon and were even heard occasionally in broadcasts.
Vinyl records can be warped by heat, improper storage, or manufacturing defects such as excessively tight plastic shrinkwrap on the album cover. A small degree of warp was common, and allowing for it was part of the art of turntable and tonearm design. "Wow" (once-per-revolution pitch variation) could result from warp, or from a spindle hole that was not precisely centered.
As a practical matter, records provide excellent sound quality when treated with care. They were the music source of choice for radio stations for decades, and the switch to digital music libraries by radio stations has not produced a noticeable improvement in sound quality. Casual ears cannot detect a difference in quality between a CD and a clean new LP played in a casual environment with background noise. There is controversy about the relative quality of CD sound and LP sound when the latter is heard under the very best conditions (see Analog vs. Digital sound argument). The limitations of recording and mastering techniques had a greater impact on sound quality than the limitations of the record itself, at least until the 1980s.
A further limitation of the record is that with a constant rotational speed, the quality of the sound may differ across the width of the record because the inner groove modulations are more compressed than those of the outer tracks. The result is that inner tracks have distortion that can be noticeable at higher recording levels.
7" singles were typically poorer quality for a variety of the reasons mentioned above, and in the 1970s the 12" single, played at 45 rpm, became popular for DJ use and for fans and collectors.
Another problem arises because of the geometry of the tonearm. Master recordings are cut on a recording lathe, where a sapphire stylus moves radially across the blank, suspended on a straight track and driven by a lead screw. Most turntables use a pivoting tonearm, introducing side forces and pitch and azimuth errors, and thus distortion in the playback signal. Various mechanisms were devised in attempts to compensate, with varying degrees of success. See more at phonograph.
Frequency response and noise
In 1925, electric recording extended the recorded frequency range from acoustic recording (168-2000 Hz) by 2½ octaves to 100-5000 Hz. Even so, these early electronically recorded records used the exponential-horn phonograph (see Orthophonic Victrola) for reproduction.
The frequency response of vinyl records may be degraded by frequent playback if the cartridge is set to track too heavily, or the stylus is not compliant enough to trace the high frequency grooves accurately, or the cartridge/tonearm is not properly aligned. The RIAA has suggested the following acceptable losses: down to 20 kHz after one play, 18 kHz after three plays, 17 kHz after five, 16 kHz after eight, 14 kHz after fifteen, 13 kHz after twenty five, 10 kHz after thirty five, and 8 kHz after eighty plays. While this degradation is possible if the record is played on improperly set up equipment, many collectors of LPs report excellent sound quality on LPs played many more times when using care and high quality equipment.
Gramophone sound suffers from rumble, low-frequency (below about 30 Hz) mechanical noise generated by the motor bearings and picked up by the stylus. Equipment of modest quality is relatively unaffected by these issues, as the amplifier and speaker will not reproduce such low frequencies, but high-fidelity turntable assemblies need careful design to minimise audible rumble.
Room vibrations will also be picked up if the pedestal - turntable - pickup arm - stylus system is not well damped.
Tonearm skating forces and other perturbations are also picked up by the stylus. This is a form of frequency multiplexing as the "control signal" (restoring force) used to keep the stylus in the groove is carried by the same mechanism as the sound itself. Subsonic frequencies below about 20 Hz in the audio signal are dominated by tracking effects, which is one form of unwanted rumble ("tracking noise") and merges with audible frequencies in the deep bass range up to about 100 Hz. High fidelity sound equipment can reproduce tracking noise and rumble. During a quiet passage, woofer speaker cones can sometimes be seen to vibrate with the subsonic tracking of the stylus, at frequencies as low as about 0.5 Hz (the frequency at which a 33-1/3 rpm record turns on the turntable).
At high audible frequencies, hiss is generated as the stylus rubs against the vinyl, and from dirt and dust on the vinyl.
Equalization
Due to recording mastering and manufacturing limitations, both high and low frequencies were removed from the first recorded signals by various formulae. With low frequencies, the stylus must swing a long way from side to side, requiring the groove to be wide, taking up more space and limiting the playing time of the record. At high frequencies noise is significant. These problems can be compensated for by using equalization to an agreed standard. This simply means reducing the amplitude at low-frequencies, thus reducing the groove width required, and increasing the amplitude at high frequencies. The playback equipment boosts bass and cuts treble in a complementary way. The result should be that the sound is perceived to be without change, thus more music will fit the record, and noise is reduced.
The agreed standard has been RIAA equalization since 1952, implemented in 1955. Prior to that, especially from 1940, some 100 formulae were used by the record manufacturers.
Recording medium comparison
Format | Typical length |
78 record | around 3 - 5 minutes per side |
45 record | often around 4 minutes (EP: 7 minutes) per side, up to 6 per side, in some cases even a few minutes longer. |
LP record | up to 30 minutes per side, though some LPs have a longer time by a few minutes. |
Audio cassette | usually 30 or 45 minutes per side, 60 minutes per side have also been sold although the tape is more prone to stretching or breaking. |
8-Track | up to 100 minutes, often 45 to 80 |
Compact disc | Earlier discs: up to 74 minutes (or up to 650 MB of data files) |
Later discs: up to 80 minutes (or up to 700 MB of data files) | |
Reel-to-Reel | 1.5
hours (both sides) if recorded at 7.5 inches per second (ips) on a standard 1800
ft reel. Professionals record at 30 ips on 3600 ft reels that will fit 22.5 minutes (one side only). A 3600 ft reel can hold up to 48 hours if recorded in mono (4 sides) at 15/16 ips. |
Minidisc | Earlier discs: 74 minutes up to 296 minutes, dependent upon compression used. |
Later discs: 80 minutes up to 320 minutes, dependent upon compression used. | |
Hi-MD | Up to 13 hours on a standard 80-minute MiniDisc. |
Up to 45 hours on a 1Gb Hi-MD (MiniDisc) | |
Digital audio player | around 17 hours per GB of data, depending on bit rate |
DVD | around 8.5 hours per layer (more if compression is used) |
SACD | |
HDDVD | |
Blu-ray | 50GB (23 Hours) |
The typical duration of a vinyl album was about 15 to 25 minutes per side, except classical music which could extend to over 30 minutes on a side. If a side exceeds the average time, the maximum groove amplitude is reduced to make room for the additional program material. This can cause hiss in the sound from lower quality amplifiers when the volume is turned up to compensate for the lower recorded level. An extreme example, Todd Rundgren's Initiation LP, with 36 minutes of music on one side, has a "technical note" at the bottom of the inner sleeve: "if the sound does not seem loud enough on your system, try re-recording the music onto tape." The total of around 40-45 minutes often influenced the arrangement of tracks, with the preferred positions being the opening and closing tracks of each side.
Although the term EP was commonly used to describe a 7" single with more than two tracks, technically they were not different from a normal 7" single. The EP used reduced dynamic range and a smaller run-off groove area to extend the playing time. However, there are examples of singles, such as The Beatles' "Hey Jude" or Queen's "Bohemian Rhapsody", which were six minutes long or more. These longer recordings would require the same technical approach as an EP. The term EP has also been used for 10" 45 rpm records, typically containing a reduced number of tracks.
Vinyl albums had a large 12" album cover, which also allowed cover designers scope for imaginative designs, often including fold-outs and leaflets.
[edit] Records in the present day
Groove recordings, first designed in the final quarter of the 19th century, held a predominant position for an impressive amount of time - just about a century - withstanding competition from reel-to-reel tape, the 8-track cartridge and the compact cassette. However, by 1988, the compact disc had surpassed the gramophone record in popularity.
In spite of their obvious flaws, such as the lack of portability, records still have enthusiastic supporters. Vinyl records continue to be manufactured and sold today, although record sales are considered to be a niche market comprised of audiophiles, collectors and DJs. Second-hand records are also available, often less than $1. Old records in particular are in much demand by collectors the world over. (See Record collecting.)
In the UK, sales of new vinyl records (particularly 7 inch singles) have increased significantly in recent years,[5][6] somewhat reversing the downward trend seen during the 1990s.
Arguments about sound fidelity
In the early days of compact discs, vinyl records were still prized by audiophiles because of better reproduction of analog recordings; however, the drawback was greater sensitivity to scratches and dust. Early compact discs were perceived by some as screechy, distorting sounds on the high end, and not as "warm" as vinyl especially in recordings that require a wide dynamic range (e.g. classical recordings). In most cases, this was the result of record companies hastily issuing CDs produced from master recordings that were compressed and equalized for vinyl. In addition the higher fidelity of compact discs revealed technical and production flaws that had been masked by the limitations of vinyl media. The poor sound quality resulted in a slower acceptance of digital music in its early years by some listeners.
Though digital audio technology has improved over the years, some audiophiles still prefer what they perceive as the warmer and more natural sound of vinyl over the harsher sound of digitals. "Natural" stated as keeping the spatial origins, sensitivity to detail, tone, clarity, richness, fullness, phase, body, timbre and dynamic range. Some listeners were also disappointed by what they considered to be unfaithful remastering of analog recordings as evidenced by low peak amplitudes, and rms power.
Proponents of digital audio state that these differences are generally inaudible to normal human hearing, and the lack of clicks, hiss and pops from digital recordings greatly improved sound fidelity. They also state that more modern anti-aliasing filters and oversampling systems used in modern digital recordings greatly reduce the problems observed with early CDs.
Most of the damage to any of the media occurs during handling: scratches, gouges, dirt, poor storage, incompatible solvents applied during cleaning or of label glue. Optical discs are not subject to physical wear during playing, whereas even a high quality pickup will wear the surface of a record and cause noticeable degradation over time. However this depends on the wear-resistance of the record itself, which is subject to the quality of the surface material used. Though neither medium is immune from damage, optical discs are more robust and modern players can play discs without noticeable problems even when scratched (Reed-Solomon error correction); a vinyl record suffering the same treatment could well be unplayable. Early on, poorly made optical disks however, are subject to a form of "wear" known as disc rot, laser rot or CD rot. This is due to the oxidation of the aluminium layer, degrading reflective properties and thus increasing the read error rate. Medical grade optical discs are estimated to have a life of 50 years for CDs, 100 years for DVDs, but they cost 10 times more than the standard grade CD | DVD. However, digital audio is increasingly stored in media-independent formats (on hard disks in flac format for example), and has a potentially infinite lifetime if regular backups are made.
The "warmer" sound of analog records is generally believed on both sides of the argument to be an artifact of harmonic distortion and signal compression by the analog system. This phenomenon of a preference for the sound of a beloved lower-fidelity technology is not new; a 1963 review of RCA Dynagroove recordings notes that "some listeners object to the ultra-smooth sound as sterile such distortion-forming sounds as those produced by loud brasses are eliminated at the expense of fidelity. They prefer for a climactic fortissimo to blast their machines"
Disc jockeys
For disc jockeys ("DJs"), mostly in the electronic dance music or hip hop genres, vinyl has another advantage over the CD — direct manipulation of the medium. DJ techniques such as slip-cueing, beatmatching and scratching originated on turntables. With CDs or compact audio cassettes one normally has only indirect manipulation options, e.g., the play, stop and pause buttons. With a record one can place the stylus a few grooves farther in or out, accelerate or decelerate the turntable, or even reverse its direction, provided the stylus, record player and the record itself are built to withstand it. Most CDJs and DJ software these days have some of these capabilities.
[edit] Creating homemade records
The record enthusiast has two choices for creating a record. There are still some studios that allow the performer the option of recording a record. A disc cutting lathe is used to transfer a sound recording to a "reference lacquer" (commonly called an acetate or dub-plate). A new form of blank disc the "vinyl blank" has been introduced with varying results.
For someone seeking to make a single record, there is the option of purchasing a recording lathe and suitable record blanks. These machines can be occasionally found on online auctions. They allow the user to cut a record, which is afterwards playable on a turntable.
The first home phonograph disk recorders were introduced by RCA Victor in October 1930. These phonographs featured a large counter-balanced tone arm with horseshoe magnet pick-up. These types of pick-ups could also be "driven" to actually move the needle and RCA took advantage of that by designing a system of home recording that used "pre-grooved" records. The material that the records were made from (advertised as "Victrolac") was soft and it was possible to somewhat modulate the grooves using the pick-up with proper recording needle and a fairly heavy weight placed on the pick-up. The discs were only six inches in diameter so recording time at 78rpm was brief. Larger size Victor blanks were introduced late in 1931, when RCA-Victor introduced the Radiola-Electrola RE-57. These machines were capable of recording at 33 1/3 rpm as well as 78 rpm. One could select to record something from the radio or one could record using the hand-held microphone. The RAE-59 sold for a hefty $350.00 at a time when many manufacturers had trouble finding buyers for $50.00 radios.
The home phonograph disk recorders of the 1930's were expensive machines that few could afford. Cheaper machines, such as the Wilcox-Gay Recordio line, were sold during the late 1940s and early 1950s. They operated at 78 RPM only and were similar in appearance to (and not much larger than) a portable phonograph of the era. One 1941 model that included a radio sold for $39.95, approximately equivalent to $500 in 2005 dollars. The fidelity was adequate for clear voice recordings.
In the past (approximately from the 1940s through the 1970s), there were booths that let the user record their own voice onto a record, when money was inserted. These were often found at arcades and tourist attractions alongside other vending and game machines. The Empire State Building's 86th floor observatory in New York City is one of the locations which had such a machine for a long time.
Currently, two companies (Vestax and Vinylrecorder) offer disk recorders priced in the high four figures which enable "experienced professional users" and enthusiasts to produce high-fidelity stereo vinyl recordings.
As an alternative, one can record to tape, cassette, computer, in analogue or digital format, depending upon the equipment capabilities.
Preservation of disc recordings
Due to the nature of the medium, playback of "hard" records, eg: LPs, causes gradual degradation of the recording. The recordings are best preserved by transferring them onto more stable media and playing the records as rarely as possible. They, in fact all, disks, need to be stored on edge in an atmosphere similar to that of human needs. The medium needs to be kept clean -- but use alcohol only on PVC or optical media, NOT on 78s. The equipment for playback of certain formats (e.g. 16 and 78 rpm) is manufactured only in small quantities, leading to increased difficulty in finding equipment to play the recordings.
Where old disc recordings are considered to be of artistic or historic interest, record companies or archivists play back the disc on suitable equipment and record the result, typically onto a digital format which can be copied and converted without any further damage to the recording. For example, Nimbus Records uses a specially built horn record player[7] to transfer 78s. However, anyone can do this using a standard record player with a suitable pickup, a phono-preamp (pre-amplifier) and a typical personal computer. Once a recording has been digitized, it can be manipulated with software to restore and, hopefully, improve the sound, for example by removing the result of scratches. It can also be easily converted to other digital formats such as DVD-A, CD and MP3.
As an alternative to playback with a stylus, a recording can be read optically, processed with software that calculates the velocity that the stylus would be moving in the mapped grooves and converted to a digital recording format. This does no further damage to the disc and generally produces a better sound than playback. This technique also has the potential to allow for reconstruction of damaged or broken disks.[8]
Notes
- Ron Penndorf. Early Development of the LP.
- Standards for Stereophonic Disc Records. Record Industry Association of America Inc. (1963-10-16).
- King Records Worldwide.
- Stereo disc recording.
- Tony Glover (2006-05-14). Back in the groove. The Business Online.com.
- Chris Hastings (2006-09-17). Why singles are top of the pops again. Telegraph.co.uk.
- Prima Voce. Nimbus Records,
- Fadeyev, V., and C. Haber (2003). "Reconstruction of mechanically recorded sound by image processing". Journal of the Audio Engineering Society 51 (December): 1172.