Glass
The materials definition of a glass is a uniform amorphous solid material, usually produced when a suitably viscous molten material cools very rapidly, thereby not giving enough time for a regular crystal lattice to form. A simple example is when table sugar is melted and cooled rapidly by dumping the liquid sugar onto a cold surface. The resulting solid is amorphous, not crystaline like the sugar was originally, which can be seen in its conchoidal fracture.
The word glass comes from Latin glacies (ice) and corresponds to German Glas, M.E. glas, A.S. glaes. Germanic tribes used the word glaes to describe amber, recorded by Roman historians as glaesum. Anglo-Saxons used the word glaer for amber.
The remainder of this article will be concerned with a specific type of glass—the silica-based glasses in common use as a building, container or decorative material.
In its pure form, glass is a transparent, relatively strong, hard-wearing, essentially inert, and biologically inactive material which can be formed with very smooth and impervious surfaces. These desirable properties lead to a great many uses of glass. Glass is, however, brittle and will break into sharp shards. These properties can be modified, or even changed entirely, with the addition of other compounds or heat treatment.
Common glass is mostly amorphous silicon dioxide (SiO2), which is the same chemical compound found in quartz, or in its polycrystalline form, sand.
Properties and Uses
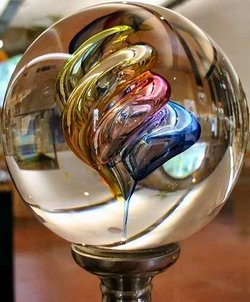
One of the most obvious characteristics of ordinary glass is that it is transparent to visible light (not all glassy materials are). The transparency is due to an absence of electronic transition states in the range of visible light, and to the fact that such glass is homogeneous on all length scales greater than about a wavelength of visible light (inhomogeneities cause light to be scattered, breaking up any coherent image transmission). Ordinary glass does not allow light at a wavelength of lower than 400 nm, also known as ultraviolet light or UV, to pass. This is due to the addition of compounds such as soda ash (sodium carbonate).
Pure SiO2 glass (also called fused quartz) does not absorb UV light and is used for applications that require transparency in this region, although it is more expensive. This type of glass can be made so pure that hundreds of kilometres of glass are transparent at infrared wavelengths in fibre optic cables. Individual fibers are given an equally transparent cladding of SiO2/GeO2 glass, which has only slightly different optical properties (the germainium contributing to a lower index of refraction). Undersea cables have sections doped with Erbium, which amplify transmitted signals by laser emission from within the glass itself.
Amorphous SiO2 is also used as a dielectric material in integrated circuits, due to the smooth and electrically neutral interface it forms with silicon.
Glass is sometimes created naturally from volcanic magma. This glass is called obsidian, and is usually black with impurities. Obsidian is a raw material for flint knappers, who have used it to make extremely sharp knives since the stone age. Obsidian collection is prohibited by law in some places (including the United States), but the same toolmaking techniques can be applied to industrially-made glass.
Glass Ingredients
Pure silica(SiO2) has a melting point of about 2000 °C (3632 °F), and while it can be made into glass for special applications (see fused quartz), two other substances are always added to common glass to simplify processing. One is soda (sodium carbonate Na2CO3), or potash, the equivalent potassium compound, which lowers the melting point to about 1000 °C. However, the soda makes the glass water-soluble, which is obviously undesirable, so lime (calcium oxide, CaO) is the third component, added to restore insolubility.
Most common glass has other ingredients added to change its properties. Lead glass, such as lead crystal or flint glass, is more 'brilliant' because the increased refractive index causes noticeably more 'sparkles', while boron may be added to change the thermal and electrical properties, as in Pyrex. Adding barium also increases the refractive index. Thorium oxide gives glass a very high refractive index, and is used in producing high-quality lenses. Large amounts of iron are used in glass that absorbs infrared energy, such as heat absorbing filters for movie projectors, while cerium can be used for glass that absorbs UV wavelengths (biologically damaging ionizing radiation).
Colors
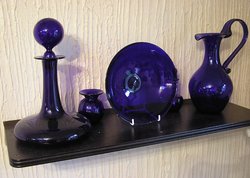
Metals and metal oxides are added to glass during its manufacture to change its color. Manganese can be added in small amounts to remove the green tint lent by iron, or in higher concentrations to give glass an amethyst color. Like manganese, selenium can be used in small concentrations to decolorize glass, or in higher concentrations to impart a reddish color. Small concentrations of cobalt (0.025 to 0.1%) yield blue glass. Tin oxide with antimony and arsenic oxides produce an opaque white glass, first used in Venice to produce an imitation porcelain. 2 to 3% of copper oxide produces a turquoise color. Pure metallic copper produces a very dark red, opaque glass, which is sometimes used as a substitute for gold ruby glass. Nickel, depending on the concentration, produces blue, or violet, or even black glass. Adding titanium produces yellowish-brown glass. Metallic gold, in very small concentrations (around 0.001%), produces a rich ruby-colored glass, while lower concentrations produces a less intense red, often marketed as "cranberry". Uranium (0.1 to 2%) can be added to give glass a fluorescent yellow or green color. Uranium glass is typically not radioactive enough to be dangerous, but if ground into a powder, such as by polishing with sandpaper, and inhaled, it can be carcinogenic. Silver compounds (notably silver nitrate) can produce a range of colors from orange-red to yellow. The way the glass is heated and cooled can significantly affect the colors produced by these compounds. The chemistry involved is complex and not well understood. New colored glasses are frequently discovered.
History of glass
Naturally occurring glass, such as obsidian, has been used since the stone age. The first documented glass making is in Egypt around 1500 BC, when glass was first used as a glaze for pottery and other items. In the first century BC the technique of blowing glass was developed and what had once been an extremely rare and valuable item became much more common. During the Roman Empire many forms of glass were created, mostly for use in vases and bottles. Glass was made from sand, plant ash and lime. The earliest use of glass was as a colored, opaque, or transparent glaze applied to ceramics before they were fired. Small pieces of colored glass were considered valuable and often rivaled precious gems as jewelry items. As time passed, it was discovered (most likely by a potter) that if glass is heated until it becomes semi-liquid, it can be shaped and left to cool in a new , solid, independently standing shape. In the first century BC, somewhere at the eastern end of the mediterranean, a new invention caused a true revolution in the glass industry. This was the discovery of glassblowing, both free-blowing and mold-blowing. The color of "natural glass" is green to bluish green. This color is caused by the varying amounts of naturally occurring iron impurities in the sand. Common glass today usually has a slight green or blue tint, arising from these same impurities. Glassmakers learned to make colored glass by adding metallic compounds and mineral oxides to produce brilliant hues of red, green, and blue - the colors of gemstones. When gemcutters learned to cut glass, they found that clear glass was an excellent refractor of light, the popularity of cut clear glass soared, that of colored glass diminished.
Glass objects from the 7th and 8th centuries have been found on the island of Torcello near Venice. These form an important link between Roman times and the later importance of that city in the production of the material. About 1000 CE, an important technical breakthrough was made in Northern Europe when soda glass was replaced by glass made from a much more readily available material: potash obtained from wood ashes. From this point on, northern glass differed significantly from that made in the Mediterranean area, where soda remained in common use.
The 11th century saw the emergence, in Germany, of new ways of making sheet glass by blowing spheres, swinging these out to form cylinders, cutting these while still hot, and then flattening the sheets. This technique was perfected in 13th century Venice.
Until the 12th century stained glass (i.e., glass with some coloring impurities (usually metals)) was not widely used.
The centre for glass making from the 14th century was Venice, which developed many new techniques and became the center of a lucrative export trade in dinner ware, mirrors, and other luxury items. Eventually some of the Venetian glass workers moved to other areas of northern Europe and glass making spread with them.
The Crown glass process was used up to the mid-1800s. In this process, the glassblower would spin around 9 lb (4 kg) of molten glass at the end of a rod until it flattened into a disk approximately 5 ft (1.5 m) in diameter. The disk would then be cut into panes. Venetian glass was highly prized between the 10th and 14th centuries as they managed to keep the process secret. Around 1688, a process for casting glass was developed, which led to its becoming a much more commonly used material. The invention of the glass pressing machine in 1827 allowed the mass production of inexpensive glass articles.
The Cylinder method was invented by William J. Blenko in the early 1900s.
Art is sometimes etched into glass via acid or other caustic substance (causing the image to be eaten into the glass). Traditionally this was done by a trained artisan after the glass was blown or cast. In the 1920s a new mold-etch process was invented, in which art was etched directly into the mold, so that each cast piece emerged from the mold with the image already on the surface of the glass. This reduced manufacturing costs and, combined with a wider use of colored glass, led to cheap popular glassware in the 1930s, which later became known as Depression glass.
Glass tools
Since glass is strong and unreactive, it is a very useful material. Many household objects are made of glass. Drinking glasses, bowls, and bottles are often made of glass, as are light bulbs, mirrors, the picture tubes of computer monitors and televisions, and windows. In laboratories doing research in chemistry, biology, physics and many other fields, flasks, test tubes, lenses and other laboratory equipment are often made of glass. For these applications, borosilicate glass (such as Pyrex) is usually used for its strength and low coefficient of thermal expansion, which gives greater resistance to thermal shock and allows for greater accuracy in laboratory measurements when heating and cooling experiments. For the most demanding applications, quartz glass is used, although it is very difficult to work. Most such glass is mass-produced using various industrial processes, but most large laboratories need so much custom glassware that they keep a glassblower on staff. Volcanic glasses, such as obsidian, have long been used to make stone tools, and flint knapping techniques can easily be adapted to mass-produced glass.
Glass art
Even with the availability of common glassware, hand blown or lampworked glassware remains popular for its artistry. Some artists in glass include Lino Tagliapietra, Sidney Waugh, Rene Lalique, Dale Chihuly, and Louis Comfort Tiffany, who were responsible for extraordinary glass objects. The term "crystal glass", derived from rock crystal, has come to denote high-grade colorless glass, often containing lead, and is sometimes applied to any fine hand-blown glass.
There are many techniques for creating fine glass art; each is suitable for certain kinds of object and unsuitable for others. Someone who works with hot glass is called a glassblower or lampworker, and these techniques are how most fine glassware is created. Glass can also be cut with a diamond saw, and polished to give gleaming facets.
Objects made out of glass include vessels (bowls, vases, and other containers), marbles, beads, smoking pipes, bongs, and sculptures. Colored glass is often used, and sometimes the glass is painted, although many glassblowers consider this crude. A significant exception is the collection of pieces by the Blaschkas.
The Harvard Museum of Natural History has a collection of extremely detailed models of flowers made of painted glass. These were lampworked by Leopold Blaschka and his son Rudolph, who never revealed the method he used to make them. The Blaschka glass flowers stand as an inspiration to glassblowers today. See the Harvard Museum of Natural History's page on the exhibit (http://www.hmnh.harvard.edu/exhibitions/glassflowers.html) for further information.
Stained glass is an art form with a long history; many churches have beautiful stained-glass windows.
Architectural glass
Float (annealed) glass
90% of the world's flat glass is produced by the float glass process invented in the 1950s by Sir Alastair Pilkington of Pilkington Glass, in which molten glass is poured onto one end of a molten tin bath. The glass floats on the tin, and levels out as it spreads along the bath, giving a smooth face to both sides. The glass cools and slowly solidifies as it travels over the molten tin and leaves the tin bath in a continuous ribbon. The glass is then fire-polished. The finished product has near-perfect parallel surfaces.
Glass is produced in standard metric sizes of 2, 3, 4, 5, 6, 8, 10, 12, 15, 19 and 22 mm.
Annealed glass is considered a hazard in architectural applications as it breaks in large, jagged shards that can cause serious injury. Building codes across the world restrict the use of annealed glass in areas where there is a high risk of breakage and injury, for example in bathrooms, in door panels, fire exits and at low heights in schools.
Plate glass
Before Pilkington's invention, flat glass panels were generally made by extrusion or rolling; the surfaces were rarely optically parallel giving rise to commonly seen distortions.
Optically parallel surfaces could be achieved by grinding and mechanical polishing, but only at considerable expense.
Cylinder glass
Glass is blown into a cylindrical iron mold. The ends are cut off and a cut is made down the side of the cylinder. The cut cylinder is then placed in an oven where the cylinder bends flat into a glass sheet. Before the introduction of the Pilkington method this was a popular method for glass manufacture. William J. Blenko used this method in the early 1900s to make stained glass.
Toughened glass
Toughened glass (also tempered glass or safety glass) is made from annealed glass via a thermal tempering process. The glass is cut to the required size and any required processing (such as polishing the edges or drilling holes in the glass) is carried out before the toughening process starts.
The glass is placed onto a roller table, taking it through a furnace which heats it to above its annealing point of 600 °C. The glass is then rapidly cooled with forced draughts of air. This rapidly cools the glass surface below its annealing point, causing it to harden and contract, while the inner portion of the glass remains free to flow for a short time. The final contraction of the inner layer induces compressive stresses in the surface of the glass balanced by tensile stresses in the body of the glass. The pattern of cooling can be revealed by observing the glass with polarized light.
Toughened glass is typically assumed to be six times the strength of annealed glass. This is because any surface flaws tend to be pressed closed by the retained compressive forces, while the core layer remains relatively free of the defects which could cause a crack to begin.
However, this strength comes with a penalty. Due to the balanced stresses in the glass, any damage to the glass edges will result in the glass shattering into thumbnail sized pieces. This is why the glass must be cut to size before toughening and cannot be re-worked once toughened. Also, ironically, the toughened glass surface is not as hard as annealed glass and is more susceptible to scratching.
Toughened glass is typically used in unframed assemblies such as frameless doors and in structurally loaded applications.
Toughened glass is considered a safety glass due to its increased strength and its tendency to shatter in small, rounded pieces which are less likely to cause injury.
Using toughened glass could pose a security risk in some situations due to the tendency the glass has to shatter utterly upon edge impact.
Though the underlying mechanism was not known at the time, the effects of "tempering" glass have been known for centuries. In the 1640s, Prince Rupert of Bavaria (1619–1682), who was grandson of James I of England, and nephew of Charles I, brought the discovery of what are now known as "Prince Rupert's Drops" to the attention of the King. These are remarkable teardrop shaped bits of glass which are produced by allowing a molten drop of glass to fall into a bucket of water, thereby rapidly cooling it. The very rapid cooling produces tremendously high tensile stress in the glass giving it unusual qualities such as the ability to withstand a blow from a hammer on the bulbous end without breaking. However, even the smallest scratch on the "tail" of the drop will allow the large amount of potential energy contained in the internal stresses of the glass to be released, causing it to explosively shatter so thoroughly that it is converted to a fine powder. The drops were often used as a practical joke, as the King would tell a subject to hold the bulb end in the palm of their hand while he broke the tip, producing a small explosion in the surprised person's hand. A video of the technique can be seen here [1] (http://www.museumofglass.org/VHS/video/rupert_drop_demo_bb.html).
Laminated glass
Laminated glass was invented in 1903 by the French chemist Edouard Benedictus. Inspired by a glass flask that had become coated with the plastic cellulose nitrate through laboratory carelessness, and then when dropped shattered but did not break into pieces, he fabricated a glass-plastic composite to reduce injuries in car accidents. However, it was not immediately adopted by automobile manufacturers, and the first widespread use of laminated glass was in the eyepieces of gas masks during World War I.
Today, laminated glass is produced by bonding two or more layers of ordinary annealed glass together with a plastic interlayer, usually polyvinyl butyral (PVB). The PVB is sandwiched by the glass which is then heated to around 70 °C and passed through rollers to expel any air pockets and form the initial bond.
A typical laminated makeup would be 3 mm glass / 0.38 mm interlayer / 3 mm glass. This gives a final product that would be referred to as 6.38 laminated glass.
The interlayer keeps the two pieces of glass bonded even when broken, and its high strength prevents the glass from breaking up into large sharp pieces.
Multiple laminates and thicker glass increases the strength. Bulletproof glass panels, made up of thick glass and several interlayers can be as thick as 50 mm.
The PVB interlayer also gives the glass a much higher sound insulation rating, due to the damping effect, and also blocks 99% of transmitted UV light.
Laminated glass is normally used when there is a possibility of human impact or where the glass could fall if shattered. Shopfront glazing and windshields are typically laminated glasses.
Laminated glass is considered a safety glass due to its ability to hold together when shattered. The shards are contained within the plastic layer that laminates the glass.
Self-cleaning glass
A recent innovation is so-called self-cleaning glass, aimed at building, automotive and other technical applications. A 50 nanometre coating of titanium dioxide on the outer surface of glass introduces two mechanisms which lead to the self-cleaning property. The first is a photocatalytic effect, in which ultra-violet rays catalyse the breakdown of organic compounds on the window surface; the second is a hydrophilic effect in which water is attracted to the surface of the glass, forming a thin sheet which washes away the broken down organic compounds.
The myth of glass being liquid at room temperature
One common urban legend is that glass is a liquid at room temperature. Supporting evidence for this position is that old windows are often thicker at the bottom than at the top. It is then assumed that the glass was once uniform, but has flowed to its new shape.
One possible source of this belief is that when panes of glass were commonly made by glassblowers, the technique that was used was to spin molten glass so as to create a round, mostly flat and even plate (the Crown glass process, described above). This plate was then cut to fit a window. The pieces were not, however, absolutely flat; the edges of the disk would be thicker due to centrifugal forces. When actually installed in a window frame, the glass would be placed thicker side down for the sake of stability. Also, the sparkle is greater and the visual effect stronger when the thicker side is down. There is anecdotal evidence that occasionally such glass has been found thinner side down, as would be caused by carelessness at the time of installation.
Writing in the American Journal of Physics, physicist Edgar D. Zanotto states "...the predicted relaxation time for GeO2 at room temperature is 1032 years. Hence, the relaxation period (characteristic flow time) of cathedral glasses would be even longer" (Am. J. Phys, 66(5):392-5, May 1998). In layperson's terms, he wrote that glass at room temperature is very strongly on the solid side of the spectrum from solids to liquids.
Evidence against glass flow
- If medieval glass has flowed perceptibly, then ancient Roman and Egyptian objects should have flowed proportionately more—but this is not observed.
- If glass flows at a rate that allows changes to be seen with the naked eye after centuries, then changes in optical telescope mirrors should be observable (by interferometry) in a matter of days—but this also is not observed. Similarly, it should not be possible to see Newton's rings between decade-old fragments of window glass—but this can in fact be quite easily done.
- Likewise, precision optical lenses and mirrors used in microscopes and telescopes should gradually deform and lose focus. This is also not observed.
See also
- Art glass
- Beveled glass
- Bulletproof glass
- Fiberglass
- Magnifying glass
- Prince Rupert's Drops
- Pyrex
- Stained glass
- Glass-reinforced plastic
References
- "Do Cathedral Glasses Flow?" Am. J. Phys., 66 (May 1998), pp 392–396
- Noel C. Stokes; The Glass and Glazing Handbook; Standards Australia; SAA HB125-1998
- Glass Beads from Anglo-Saxon Graves: A Study on the Provenance and Chronology of Glass Beads from Anglo-Saxon Graves, Based on Visual Examination (http://www.oxbowbooks.com/bookinfo.cfm/ID/36444/MID/11027) by Birte Brugmann
External links
- Corning Museum of Glass (http://www.cmog.org/), especially Research, Teach, and Learn section.
- Is glass liquid or solid? (http://math.ucr.edu/home/baez/physics/General/Glass/glass.html) by Philip Gibbs on the spr USENET physics FAQ
- Antique windowpanes and the flow of supercooled liquids (http://dwb.unl.edu/Teacher/NSF/C01/C01Links/www.ualberta.ca/~bderksen/windowpane.html)
- article on the non-flowness of glass (http://dwb.unl.edu/Teacher/NSF/C01/C01Links/www.ualberta.ca/~bderksen/florin.html)
- Page devoted to the AFU glass flow controversy, with links to citations (http://tafkac.org/science/glass.flow/)
- Page stating that glass does not flow (http://www.glassnotes.com/WindowPanes.html)
- Substances used in the Making of Colored Glass (http://1st.glassman.com/articles/glasscolouring.html)
- Self-cleaning glass (http://www.activglass.com/index_eng.htm) - Product information from Pilkington.